Calibrating Pressure Sensors: Best Practices
Properly calibrated sensors are essential for quality control, safety, and data accuracy, making them indispensable in various fields, from industrial processes to healthcare and environmental monitoring.
GENERAL INTRUDUCTION
2 min read
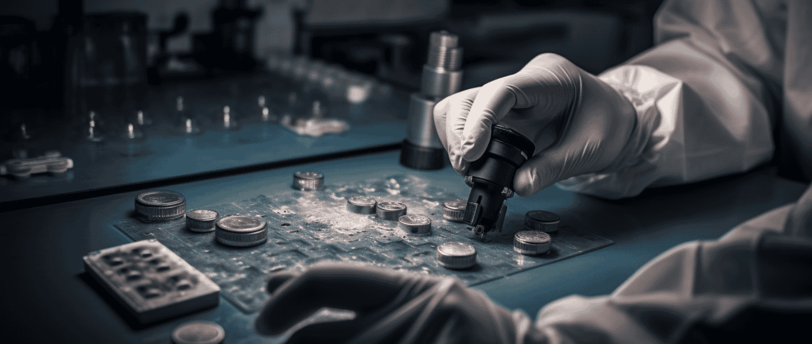
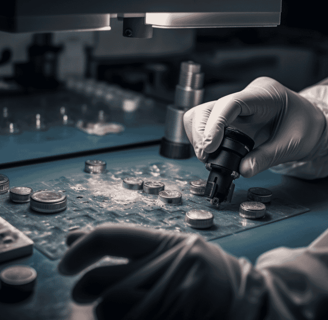
Calibrating pressure sensors is a critical step to ensure that they provide accurate and reliable measurements. Calibration is the process of comparing a sensor's output to a known reference standard to make necessary adjustments. In this article, we'll explore the best practices for calibrating pressure sensors, regardless of the application or industry.
1. Understand Calibration Basics
Before you begin the calibration process, it's essential to understand some fundamental concepts:
Accuracy: The goal of calibration is to improve a sensor's accuracy, ensuring that its measurements match a known reference standard.
Calibration Standard: You will need a calibration standard, which is a device or instrument with a known and traceable pressure value. This standard is used to compare and adjust the sensor's output.
Calibration Range: Determine the range over which you will calibrate the sensor. This should cover the pressure values typically encountered in your application.
2. Choose the Right Calibration Equipment
Selecting the appropriate calibration equipment is crucial. Consider the following factors:
Calibration Standard: Ensure that the calibration standard is accurate, traceable, and regularly maintained. It should cover the desired pressure range.
Calibration Pump: A pressure source, such as a hand pump or pressure generator, is required to apply known pressures to the sensor. Choose one with high precision and stability.
Data Acquisition System: An accurate data acquisition system is essential to record the sensor's output during calibration.
3. Prepare the Sensor and Equipment
Before calibration, you should:
Inspect the sensor for physical damage or contamination. Clean or repair it if necessary.
Stabilize the sensor and equipment at the desired calibration temperature, as temperature can affect pressure readings.
4. Perform Calibration at Multiple Points
Calibrate the sensor at multiple points within the chosen calibration range. This helps identify any non-linearity or hysteresis in the sensor's response. For instance, if your sensor has a range of 0-100 psi, calibrate it at various pressures, such as 10 psi, 50 psi, and 90 psi.
5. Record and Document Results
During calibration, record the sensor's output readings at each calibration point. Document these readings along with the corresponding reference values and the calibration date. Proper documentation is crucial for traceability and quality control.
6. Calculate and Apply Corrections
Using the recorded data, calculate correction factors or coefficients to adjust the sensor's output. Apply these corrections to the sensor's output signal to bring it in line with the reference standard.
7. Verify Calibration
After applying the corrections, re-check the sensor's output against the calibration standard to ensure that it now provides accurate measurements. This step helps validate the effectiveness of the calibration.
8. Regular Maintenance
Calibration is not a one-time process. To maintain accuracy, sensors should be recalibrated at regular intervals, as specified by the manufacturer or industry standards. Additionally, if a sensor undergoes physical shock or experiences environmental changes, it may require re-calibration.
Conclusion
Calibrating pressure sensors is a critical practice to ensure accurate and reliable measurements. By following these best practices and understanding the basics of calibration, you can maintain the precision of your pressure sensors, regardless of the application or industry. Properly calibrated sensors are essential for quality control, safety, and data accuracy, making them indispensable in various fields, from industrial processes to healthcare and environmental monitoring.